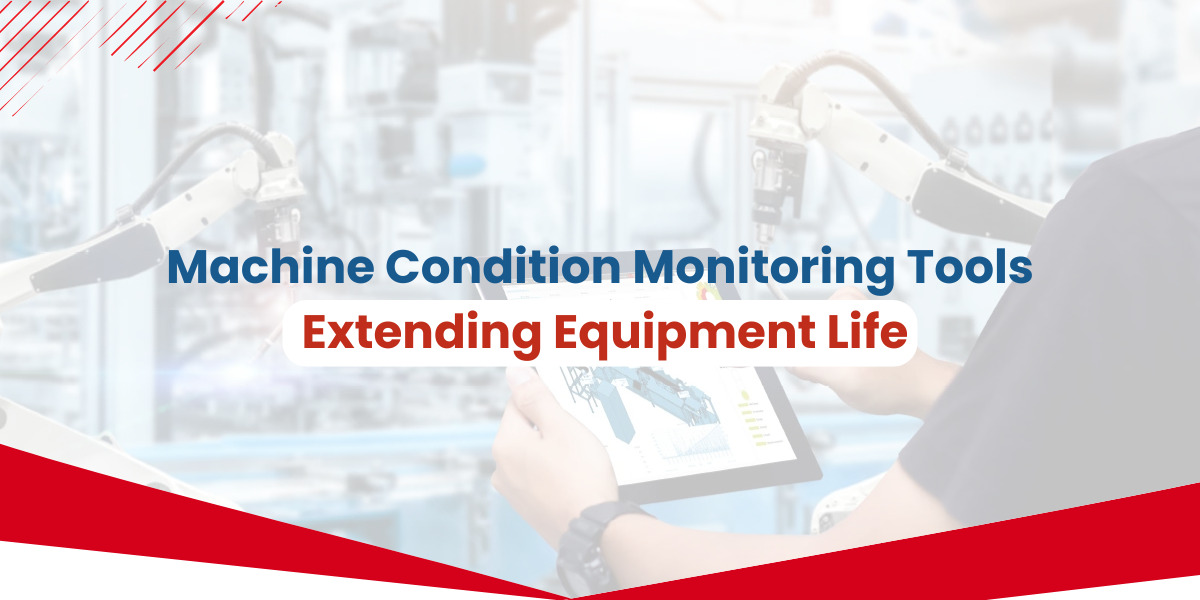
Machine Condition Monitoring Tools: Extending Equipment Life
In the fast-paced world of industrial operations, the longevity and reliability of machinery are paramount. Every piece of equipment, from the smallest pump to the largest turbine, represents a significant investment, and its uninterrupted operation is crucial for productivity and profitability. This is where Machine Condition Monitoring (MCM) Tools come into play. Far beyond simply reacting to breakdowns, MCM offers a proactive approach, providing invaluable insights into the health of your assets, enabling you to extend their operational life and enhance overall plant efficiency.
At its core, machine condition monitoring involves continuously or periodically assessing the physical state of machinery to detect early signs of potential issues. By identifying anomalies before they escalate into critical failures, businesses can transition from reactive maintenance (fixing things after they break) to predictive maintenance (fixing things before they break). This shift not only prevents costly unplanned downtime but also optimizes maintenance schedules, reduces repair expenses, and significantly extends the lifespan of valuable equipment.
The Foundation of Predictive Maintenance: How MCM Works
Machine condition monitoring relies on a suite of sophisticated tools and techniques that collect data from various parameters, providing a comprehensive picture of an asset’s operational health. This data is then analyzed to identify deviations from normal operating conditions, signaling potential wear, damage, or impending failure.
Here’s a closer look at the key condition monitoring techniques:
- Vibration Analysis:
- What it is: This technique measures the vibrations produced by rotating machinery. Every piece of rotating equipment generates a unique vibration signature. Changes in this signature often indicate underlying issues.
- How it works: Sensors, typically accelerometers, are strategically placed on machinery to capture vibration data. This data is then processed to analyze parameters like amplitude, frequency, and waveform.
- What it detects: Imbalances, misalignment, bearing faults, gear wear, looseness, and other mechanical defects. Early detection of these issues allows for targeted repairs before they lead to catastrophic failure.
- Benefits: Reduces unexpected breakdowns, prolongs bearing and gear life, improves machine reliability, and enhances operational safety.
- Thermography (Infrared Imaging):
- What it is: Thermography involves using infrared cameras to detect and visualize heat patterns. Abnormal heat signatures can indicate friction, electrical resistance, or other energy losses.
- How it works: An infrared camera captures the thermal radiation emitted by equipment surfaces, converting it into a visual heat map. Hot spots or unusual temperature distributions are then analyzed.
- What it detects: Overheated bearings, faulty electrical connections, motor winding issues, insulation defects, steam trap failures, and fluid leaks.
- Benefits: Prevents electrical fires, identifies overloaded circuits, minimizes energy waste, and ensures the efficient operation of thermal systems.
- Oil Analysis:
- What it is: This technique involves periodically taking samples of lubricating oils and hydraulic fluids for laboratory analysis.
- How it works: Specialized tests are performed on oil samples to assess their physical and chemical properties, detect contaminants, and identify wear particles.
- What it detects: The presence of metals from wear (indicating component degradation), fuel or coolant contamination, oxidation, viscosity changes, and additive depletion.
- Benefits: Extends lubricant life, identifies abnormal wear patterns in engines and gearboxes, prevents component failure, and reduces maintenance costs associated with unnecessary oil changes.
- Acoustic Analysis (Sound Monitoring):
- What it is: This involves monitoring the sound waves emitted by machinery. Changes in sound patterns can indicate anomalies.
- How it works: Microphones or acoustic sensors are used to capture the operational sounds of equipment. Sophisticated software then analyzes these sound patterns for deviations.
- What it detects: Leaks (air, gas, vacuum), cavitation in pumps, arcing in electrical systems, or unusual noises from bearings and gears.
- Benefits: Ideal for detecting issues in hard-to-reach areas, provides non-intrusive monitoring, and can identify problems that may not yet manifest as vibration or heat.
- Electrical Monitoring:
- What it is: This focuses on analyzing electrical parameters of motors and other electrical components.
- How it works: Sensors and meters are used to monitor current, voltage, power factor, and other electrical signatures.
- What it detects: Imbalances in electrical currents, stator or rotor faults in motors, insulation degradation, and power quality issues.
- Benefits: Prevents motor failures, optimizes energy consumption, and enhances the safety of electrical systems by identifying potential hazards.
Beyond the Tools: The Holistic Approach
While individual MCM tools are powerful, their true potential is unlocked when integrated into a holistic monitoring program. This often involves:
- Data Integration: Combining data from various monitoring techniques provides a more comprehensive view of equipment health. For instance, a rise in vibration (vibration analysis) coupled with an increase in bearing temperature (thermography) paints a clearer picture of a failing bearing.
- Trending and Analysis: Regular collection and trending of data allow maintenance teams to track the progression of a fault and predict when intervention will be necessary. This moves maintenance from a reactive to a predictive model.
- Alarming and Alerting: Setting up automated alerts based on predefined thresholds ensures that maintenance personnel are immediately notified when a parameter deviates from its normal range, allowing for timely action.
- Expert Interpretation: While software provides valuable analysis, the insights of experienced technicians and engineers are crucial for accurate diagnosis and effective decision-making. Their expertise helps differentiate between minor anomalies and critical issues.
The Tangible Benefits: Why Invest in MCM?
Investing in machine condition monitoring tools and programs offers a multitude of benefits that directly impact an organization’s bottom line and operational stability:
- Extended Equipment Lifespan: By addressing small issues before they become major problems, MCM significantly reduces wear and tear, allowing machinery to operate optimally for longer periods. This defers capital expenditure on new equipment and maximizes the return on existing assets.
- Reduced Unplanned Downtime: The ability to predict failures means that maintenance can be scheduled during planned shutdowns or off-peak hours, minimizing disruptions to production. This dramatically increases operational uptime and overall productivity.
- Lower Maintenance Costs: Predictive maintenance eliminates the need for expensive emergency repairs and reduces the frequency of routine, time-based maintenance that might be unnecessary. Parts are ordered only when needed, minimizing inventory costs.
- Enhanced Safety: Detecting faults like overheating or excessive vibration prevents potential equipment failures that could lead to accidents, injuries, or environmental damage, creating a safer working environment.
- Optimized Performance: Healthy machinery operates more efficiently. By maintaining equipment in peak condition, MCM helps ensure consistent product quality and optimized energy consumption.
- Improved Planning and Budgeting: With clearer insights into equipment health, maintenance managers can forecast future repair needs and allocate resources more effectively, leading to more accurate budgeting.
Partnering for Success: Choosing the Right MCM Solutions
For industries across India, from manufacturing and power generation to oil and gas, integrating effective machine condition monitoring tools is no longer a luxury but a strategic imperative. Companies like VPEL, as authorized dealers and suppliers of leading brands such as Honeywell, Emerson, Siemens, and Yokogawa, offer a comprehensive range of instrumentation and control solutions, including advanced MCM tools.
Whether you are looking for industrial vibration analyzers, sophisticated thermography cameras, or robust oil analysis kits, selecting a knowledgeable partner is crucial. A reliable supplier not only provides quality products but also offers the expertise and support needed to implement and optimize your condition monitoring program for lasting success.
By embracing machine condition monitoring, businesses can unlock greater operational efficiency, reduce costs, enhance safety, and ultimately, ensure that their valuable equipment continues to perform at its best, extending its life and contributing to sustained growth.